How SIPOC Fits Into Your MO?
If you are relatively new to the world of Operational Excellence (OEx), the concept of SIPOC would be one of those tools that will be introduced early on in your induction courses. And as with many other OEx tools, SIPOC is yet another simple but powerful approach normally used to solve various operational and organizational problems.
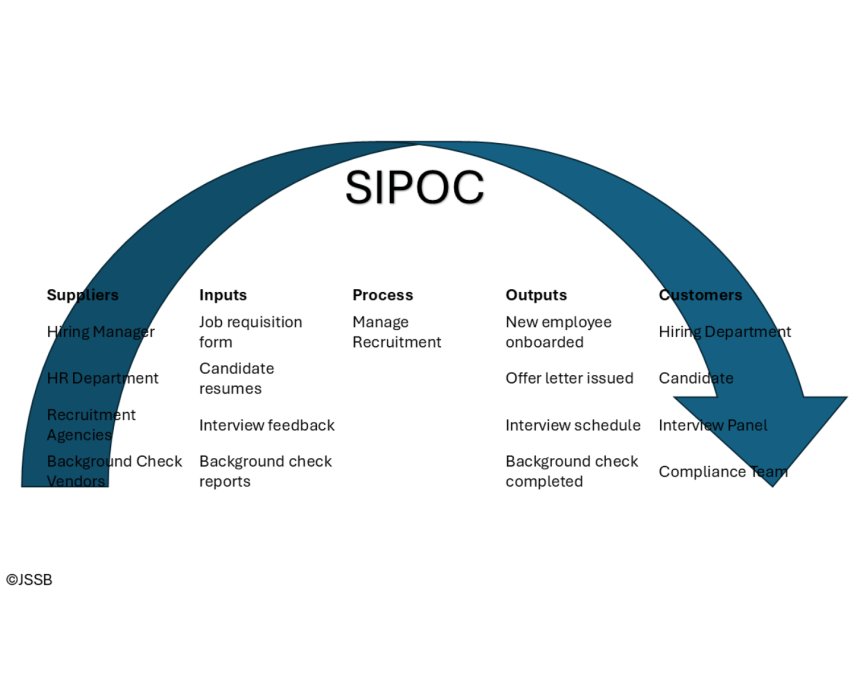
If you are relatively new to the world of Operational Excellence (OEx), the concept of SIPOC would be one of those tools that will be introduced early on in your induction courses. And as with many other OEx tools, SIPOC is yet another simple but powerful approach normally used to solve various operational and organizational problems.
In the context of Manpower Optimization (MO), our 5-Step methodology incorporates SIPOC as a critical component to comprehensively capture all of the relevant work processes that make up both, the routine and non-routine deliverables of the functions as mapped in the organization's Key Value Chain. It is through this, we will be able to directly and systematically see the real picture of what constitutes the deliverables of those functions which later, will ultimately be the very basis of our MO.
What is SIPOC?
Although the word may remind some of us of 'cyborgs', SIPOC is not even a close cousin to them. It is actually an acronym that consists of 5 elements as listed here;
S = Supplier
I = Input
P = Process
O = Output
C = Customer
So, how to use this? Well, it is quite straightforward. After we have exhaustively listed down all of the routine and non-routine work processes of the function in question, say, Human Resource or HR, what we need to essentially do is to carefully dissect each of these processes using the above SIPOC keywords.
Let us take the recruitment process as an example which is certainly a cornerstone HR responsibility. Now, we need to populate the SIPOC diagram accordingly. First, let us begin by naming the work process under study in the PROCESS column in the middle. In this case, we should put ‘Manage Recruitment’ in that column.
Next, we need to deliberate on all of the OUTPUT expected from the process together with the CUSTOMERS who would require those outputs. In this case, one of the possible outputs for the recruitment process would be, ‘new recruit on board’ and the corresponding customer for this would be most definitely the specific department that requires the new recruit.
After this, we need to turn our attention to the INPUT column on the left-hand side of the SIPOC diagram. Here, we need to deliberate on what are the required documents, request forms or perhaps certain approval in order to kick-start the recruitment process in the first place. Simultaneously, we have to identify the SUPPLIERS of all those inputs.
In other words, we actually do SIPOC by starting from P (process), later O (output) & C (customers) and finally, with I (input) & S (suppliers). Despite the name, SIPOC, we actually in practice do POCIS instead or even sometimes, COPIS (Start from Customer, Output, Process, Input, Supplier) if the context requires a more customer-focused analysis.
As you can see, by completing SIPOC for all of the functional work processes, we will immediately have an integrated view of all the required INPUTS to complete the work PROCESSES coming from the SUPPLIERS as well as the corresponding expected OUTPUTS to be delivered/submitted to both internal and external CUSTOMERS. With such rich and detailed data of the functional work processes, this will give us an invaluable insight into all the key components of the deliverables expected from the function under study.
It is quite fascinating to see how such a humble tool like SIPOC can actually generate such an elaborate set of results on our work processes. However, this is not even 20% of the whole story.
This is because the SIPOC in itself can hardly be prescriptive for us to later quantify the amount of process time required to complete each of the work processes (This data is important for us to later evaluate the FTE which will be covered in a separate posting). In order to achieve this, we need yet another OEx tool which is commonly known as ICOR.
What is ICOR?
ICOR is essentially an acronym for;
I = Input
C = Control
O = Output
R = Resource
Simply put, ICOR is in actuality a continuation analysis of the previous SIPOC. Since, we only define a generic name for the process (in this case, Manage Recruitment), we will have to deliberate each of the listed work processes using ICOR.
The first INPUT and final OUTPUT in ICOR will be the same INPUT and OUTPUT as deliberated in SIPOC whereas the intermediate INPUT/OUTPUT in ICOR will depend on the steps relevant to the specific work process.
To start ICOR analysis, we will have to cluster all of the steps to complete this recruitment process as currently practiced in our organization into approximately 6-7 or fewer key steps. Do take note that ICOR should never be a verbatim reproduction of the SOP or even the work instruction. Each of these key steps will be further scrutinized based on the above ICOR keywords.
In fact, ICOR should ideally represent the higher level steps to complete the work processes in question. Each of these clusters or this higher-level step is essentially an agglomeration of other smaller steps governed by a particular SOP or work instruction. It is these SOPs and work instructions that will be specified in the Control section of our ICOR.
The Resource part of the ICOR is for us to list down the person/s responsible for carrying out the key steps as well as those who need to monitor or approve them. So, if say, the key step here for recruitment process is 'Evaluate job specification', the appropriate resource here should normally be the HR executive with approval from the corresponding manager.
As we do ICOR for each step, we are effectively inventorizing all of the relevant SOPs and work instructions for the key steps together with the responsible parties who need to execute & monitor those steps in question.
So, what is next?
Once, we have methodically furnish our SIPOC and ICOR comprehensively, now it is time to visualize the whole process in a way that would ease our overall understanding of the work processes. We do this by constructing a deployment chart (DC) i.e the line of visibility of the whole process based on our completed ICORs.
It is here that we will assign the prevailing process time for each of the processes' key steps based on our interview from the responsible parties who are executing the job specifically.
With all of these detailed data from SIPOC, ICOR and DC, we will be able to see a complete and integrated model of how our current functional work processes are operating.
At JSSB, we call this document that combines SIPOC, ICOR and DC in one place as Job Performance Manual or JPM in short. This JPM is basically the organization's operational model embodied in a one-stop document.
With such powerful document at your disposal, you can easily evaluate areas of your operations which can be further optimized and improved. You can also easily see avenues where you can abolish certain unnecessary, non-value-adding steps in the work processes. You may also decide that certain repetitive steps be combined or even re-arranged to deliver better output and outcome. This is how powerful JPM is if used intelligently.
It is through all these rich set of data that we will be able to proceed in our MO process in the next phase. These results from SIPOC, ICOR and DC will most definitely facilitate us in evaluating the right-sizing for our organization which is at the heart of any MO exercise.
As you may have correctly observed, the whole SIPOC, ICOR and DC process is indeed tedious so as to generate a meaningfully-detailed account of all of the functional work processes. Nevertheless, rest assured that the results from such meticulously-analyzed document will undeniably provide you with a rock-solid foundation for an effective MO in the organization.
Share






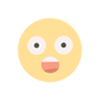